About
This module encloses the whole process of production including planning,
coordinating of sales, supplying and manufacturing activities, calculations and scheduling at the facility. This rounded system gives you answers to all output prices delivery datelines, it alleviates production file and report records, enables the optimisation of stock and manufacturing hours and it ensures fast “what-if” simulations.

Important module characteristics are:
- the definition of complex and multi- level cost sheets with multiple production procedures
- the definition of technology alternatives, the possibility of creation of ad-hoc cost sheet modifications, launching of unique orders without technological templates
- automated launch of production orders based on orders and plans
- material and parts reservation
- the generation of production documentation
- the traceability is ensured by series/material batches and finished products monitoring
- the fast MRP algorithm with the possibility of repeated generation of new plans, based on the updated progress report and stock level
- the detailed monitoring of the production activity, reports on the work completion, reports on waste
Production accounting at actual production cost:
- the complex formulas for gathering and allocation of overhead cost
- a multiple key system for a precise overhead cost allocation
- an iterative algorithm for the elimination of the stock variance
- all account phases are fully automatic
- the calculation of the production cost structure for complex products with a cascade price structure printouts for all built in semi products
- integration with the Opcenter APS system, world's leading software manufacturer for planning and production scheduling
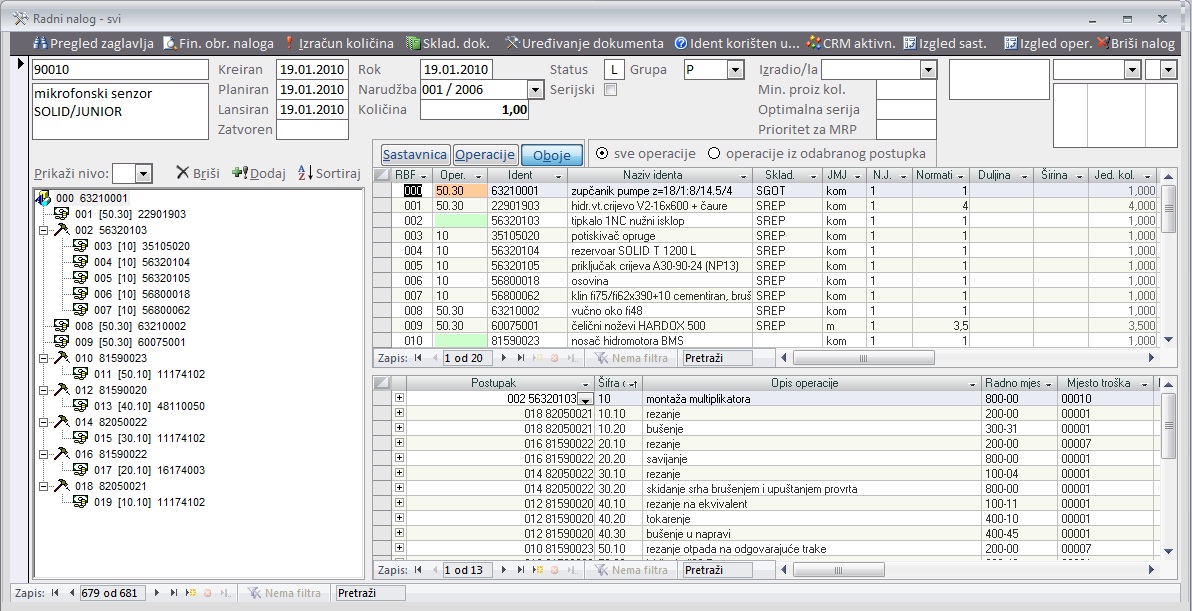